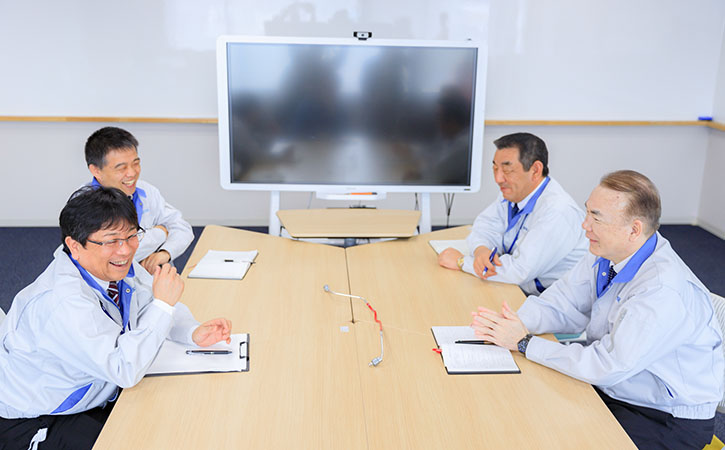
Cross Talk
製品紹介
(開発プロセス座談会)
USUIの“未来”をつくる、終わりなきモノづくりへの挑戦
FCV用高圧水素配管プロジェクト
開発・設計から量産まで足掛け5年を要した水素自動車用の高圧水素配管の製造プロジェクト。
当社の世界シェアトップ製品で培った高い技術力を評価され、顧客からの信頼の証として始まったプロジェクトでしたが、
そこにはこれまでに直面したことのない困難の数々が待っていました。
当時、営業・設計・開発・製造の各立場で関わった4人から、苦労やUSUIのモノづくりに関する姿勢を語ってもらいました。
-
深澤 正人
1992年入社
営業本部
グローバルセールス 5部 -
堤 信吾
1985年入社
製造本部
初期管理部(設計) -
林 耕一
1998年入社
開発本部
商品企画部 -
渡邊 享
1993年入社
製造本部
富士御殿場製造部
※表記は当時の配属部署
「世の中にないものを創る」- 数々の苦難を乗り越えた、貴重な挑戦の足跡
- 林
-
それまで世の中の誰も知らなかった、日本初の水素自動車の開発プロジェクトに携わったメンバーが集まったわけですが、我々が知っているガソリンやディーゼルとは何から何まで異なり、すべてが初めて直面することばかりでしたね。
特に燃料の水素が700気圧という高圧になること。これが最大の焦点になりました。
- 深澤
-
扱う流体が水素という超高圧の気体ですから、ガソリン・ディーゼル用の配管とは異なり、高圧水素が漏れないようにシールするための方策、特に接続部への対処がネックでしたね。
最初にオーダーを受けたのは私の前任者で、お客様から当時350 気圧だったものを700気圧に上げたいのだが、「臼井の豊富なノウハウを活かしてその圧に耐えられるパーツの開発を実現できないか」という話だったんですね。
- 林
-
要するにもっと水素を積みたいが空間は限定されている。ついてはさらに圧を上げようということなんですが、700気圧を扱うための規格さえなかった中での開発でしたから、本当にシビアなオーダーでしたよね。
もともと当社は高圧のパイプを得意としていて、その確かな信頼があったからこそお客様から頼りにされたわけですが。
すべての工程を、1ランク上の規格に引き上げるために
- 堤
- 設計については私の上司をリーダーとして一緒に計画を進めたのですが、「ガソリンやディーゼルと700気圧の水素はまったく違うぞ」と何度も言われました。
- 渡邊
-
パイプの先端、他のパーツとの接続部ですね。ゴムや樹脂を使えばシールはしやすいのですが、700気圧の高圧下ではゴムや樹脂などの材料は耐えられない。
しかし液体ならともかく、金属同士の接続部を高圧の気体がもれないように完全にシールするのは至難の業ですよね。
- 堤
-
この高圧には従来のシール技術では対応できないため、あらゆる技術をもう一段階上のレベルに引き上げなければならない。
具体的にはシール部の面粗度を引き上げなければ、要求品質を到底実現できないことから、上司とともにドイツに飛んで、より高度な面粗度へと改良するための設備を視察し、当社の設備・環境にどうしたら導入することができるかの検討を行いました。
- 林
-
そこが最大の課題でしたね。
もちろんこれまで手掛けたことがない事例なので、どんな条件で締め付け、どういう表面状態にするべきなのかを、一つ一つ手探りで見つけていくしかなかったですから。
- 堤
- 設計と開発が部署を超えて一体になり、この課題の解決に向けて試行錯誤を繰り返す毎日でしたね。
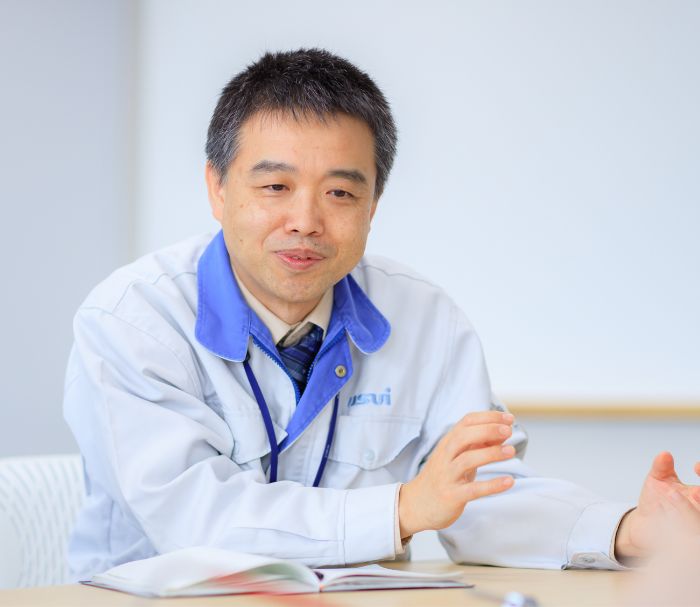
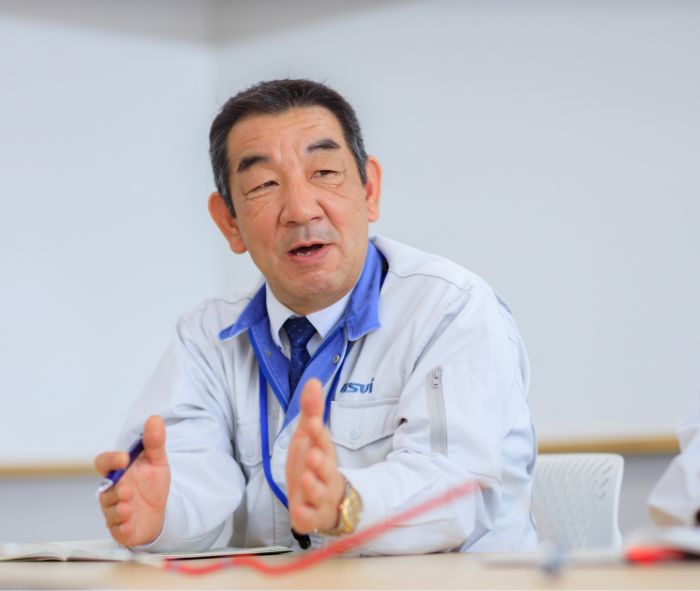
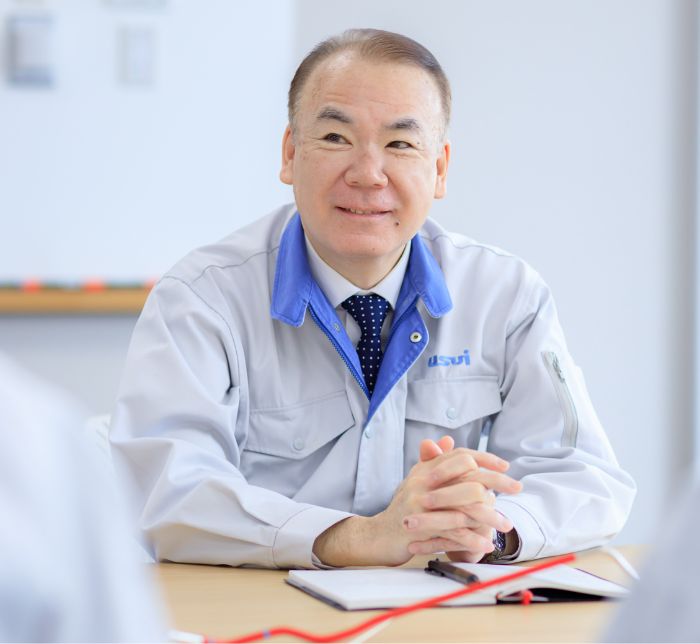
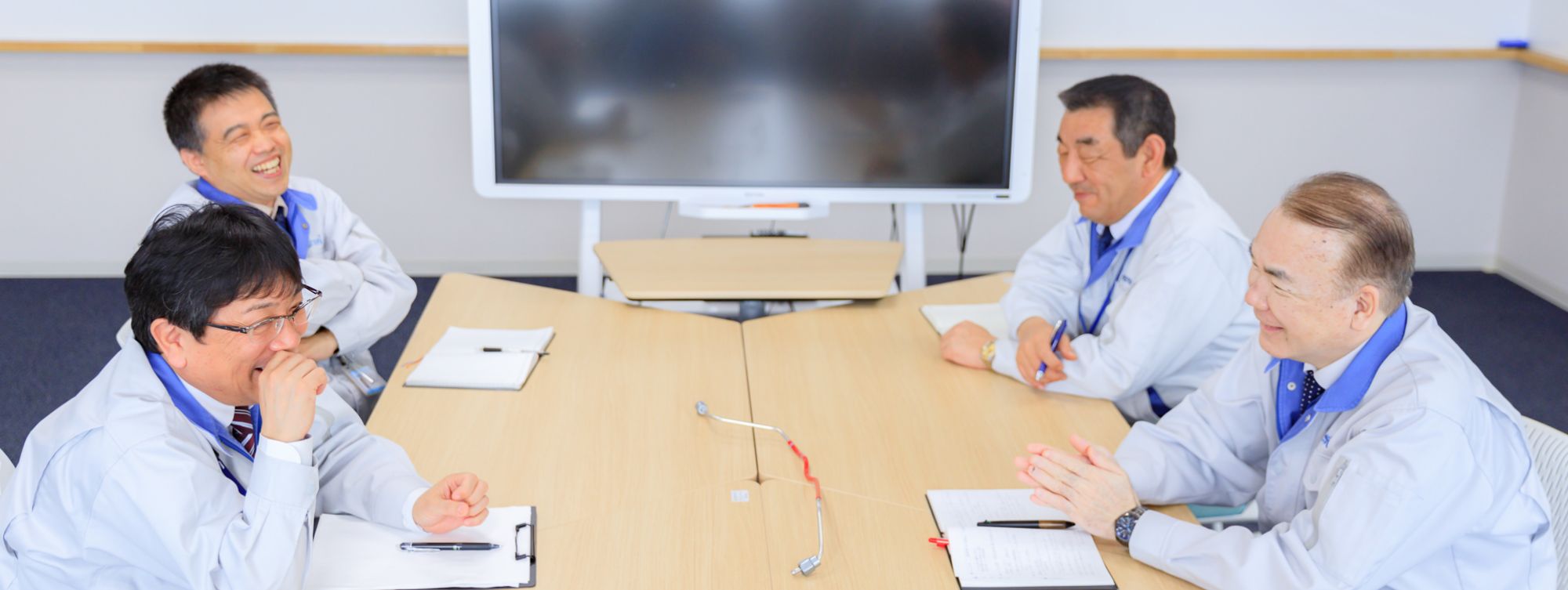
お客様もパーツ開発者も、全員が手探りの中で
- 深澤
-
お客様との打ち合わせは、つねに設計・開発とセールスの三者体制。
お客様側も手探り、こちらも未知の領域という中で、提示される数々の困難なオーダーをどう調整していくかが私のセールスとしての役割でした。
これが将来どんなビジネスに成長するのか、売上面での期待も未知数でしたから、社内の調整にも苦労しました。
各部署からのそれぞれの意見が衝突することも多々あったので、「一緒に頑張ろうよ」と皆をなだめながらね(笑)。
- 堤
- 振り返ってみると、よく通いましたよね。
- 林
-
先行している水素自動車もなく、お客様も試作したことこそあれ、量産の経験はありませんでした。
大量の開発資金をつぎ込んで作った試作品は一般の方が購入できる価格ではありませんから、この試作品と同等のクオリティが、本当に市販車に必要なのかという議論もありました。
またお客様側の水素自動車の担当者もいわゆる研究者で、価格などに対する認識も量販担当者の常識とは大きな隔たりがあり、量産化を前提とした共通認識を形成するまでにはかなりの時間がかかりました。
- 堤
-
お客様に対してだけでなく、当社と材料メーカーさんとの間でもそれは同様でしたね。
技術面・価格面などお互いの主張のせめぎ合いの中で、新たな協業体制を構築するのには本当に難しいです。
- 渡邊
-
試作ではなく市販車としての製造ラインに乗せるためには、新しい設備や治具が必要になるんですが、それを整備するには資金が必要になる。でも肝心な売れ行きが不透明だから設備投資もできず、結局はすべてが手作業に頼らざるを得ないというのが製造部門の悩みでした。
例えばパイプの中にアルコールを流して洗浄する際にもキッチンタイマーで時間を測りながら手作業したり、パーツの形状を一つ一つ画像測定機で測ったりと、すべて作業者の手が頼りでしたね。
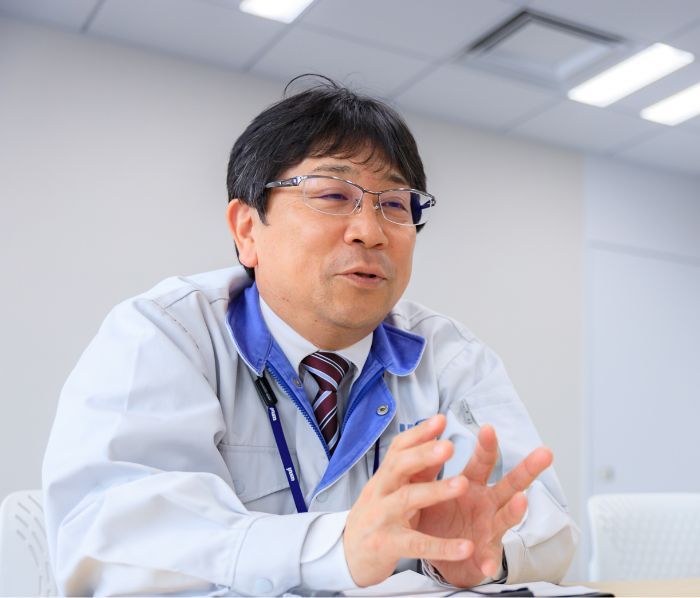
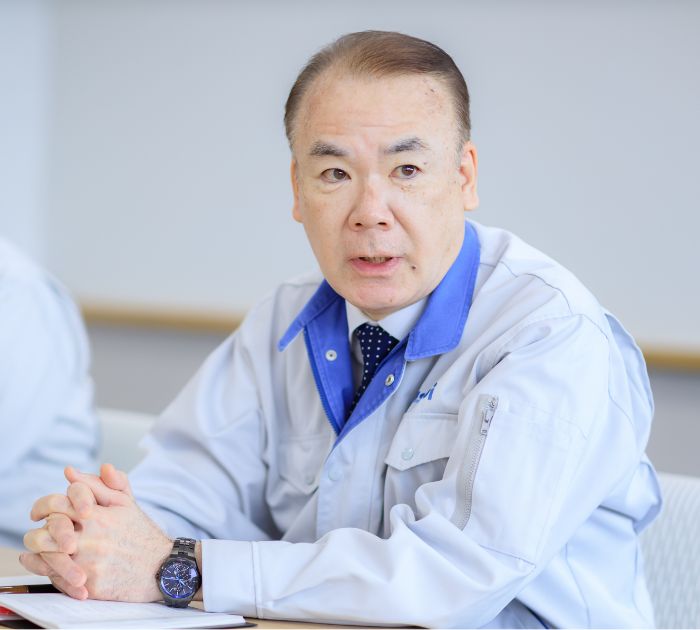
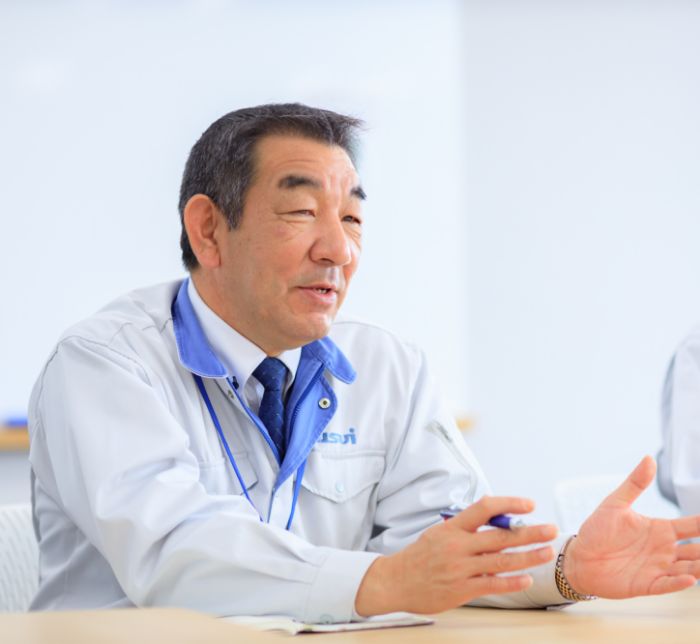
明かりの見えない、漏れとの戦い
- 渡邊
-
そんな試作段階を経て少しずつ量産の準備が進んでいく中でも、お客様からは都度都度、漏れの情報が入ってきました。
接触部の金属表面のごく微小な隙間から高圧水素が漏れてしまうんですが、これは当社の技術の問題ではなくパイプそのものの問題なんですね。
- 林
-
パイプの接続に関しては、継ぎ先となる別パーツを製造している他社さんが関わってきますが、相手先としても非常に機密性の高い情報なので詳細なデータを出してくれないんですよね。
お客様が取りまとめてはくれるものの、相手方の製品やデータを精査することができないのは致命的な問題でした。
しかもこの両パーツの締め付け作業を行う人も介在するわけで、お客様から漏れの報告とその原因究明を依頼されても、当社以外の要因については解明することができないというもどかしさを感じましたね。
- 堤
- 問題の原因は、自分たち以外のところにあるわけですからね。
- 渡邊
-
試作の手法で量産品を製造するという、まさに手作り・モノづくりを地で行くような苦労の連続でしたね。
ただこういうユニークな作業工程だったため、対外的には当社の技術力を理解していただきやすかったですね。
今思い出したんですが、視察のお客様に「700気圧というのはスペースシャトルの打ち上げ時よりも高圧なのだそうですよ」とお話するとたいそう驚かれて「ちなみにスペースシャトルの圧力はどのくらいなんですか?」と逆に尋ねられ、こちらも詳しい数字まではさすがに答えられず恥ずかしい思いをしたこともありました(笑)。
鋼管の製造に伴う、微小な内面傷の課題をクリア
- 渡邊
-
パイプの内側の傷への対処も重要なポイントでした。
700気圧の高圧下では内側にほんのわずかな傷があってもバーストの危険があるんですよね。
- 林
-
パイプそのものの製造工程に起因する顕微鏡レベルでの微小な傷は避けられないものの、安全に関わることですから、お客様も特に神経を尖らせて「傷ゼロ」を要求します。
もちろんこちらとしても「ゼロ」を目指すのですが、その反面、完全な「ゼロ」というのは実現不可能で、ある意味では世の中に存在しないものを要求されているとも言えます。
お客様側の求めるゼロ精度への挑戦と、現実的に実現可能な精度との綱引きですね。
- 堤
- そこは設計としても対処しようがない部分ですね。
- 渡邊
- 材料自体の品質に起因する問題なので、設計としても対処のしようがない問題ですからね。
- 林
-
シームレスパイプは大元になる大きな中空のビレットを加熱延伸して製造しますが、お客様側の要求精度がどれだけ実現困難なのかを理解してもらうために、ビレットの製造現場である鉄鋼会社まで一緒に確認しに行ったこともありました。
そんな折衝を続けながらお客様が要求するギリギリの許容限界値を精確に見定め、製造工程の改善で限界値をクリアする方策を煮詰めていったのですが、これには本当に膨大な時間と手間を要しました。
- 渡邊
- こうしたステップを経て少しずつ製造方法が固まっていきましたが、製造だけでなく完成後の製品へのホコリの付着も大敵でしたから、クリーンルームに入れたりと保管にも製造と同じくらいに神経を使いましたね。
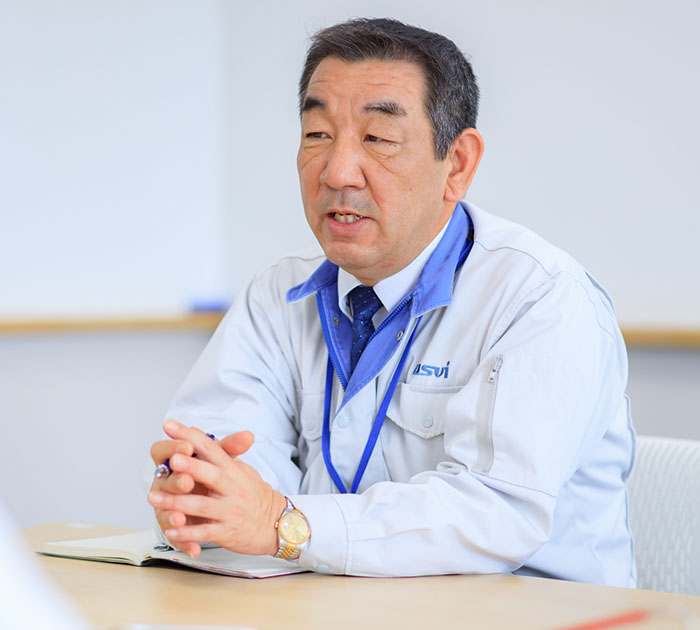
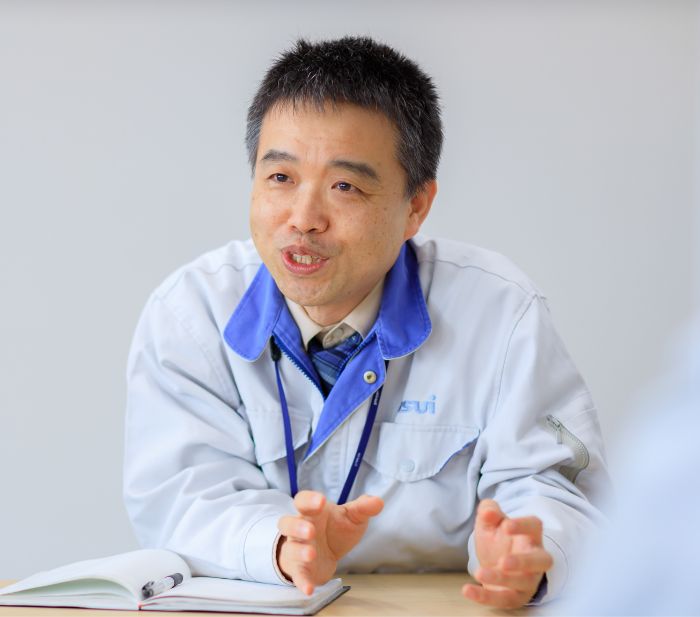
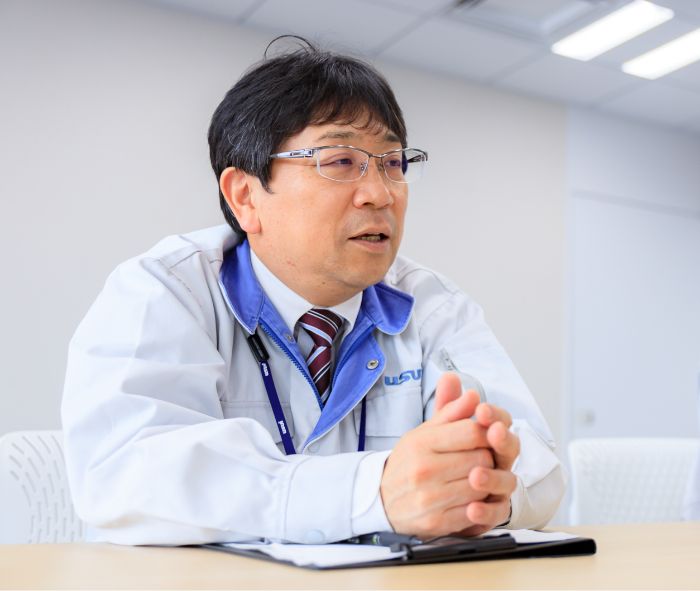
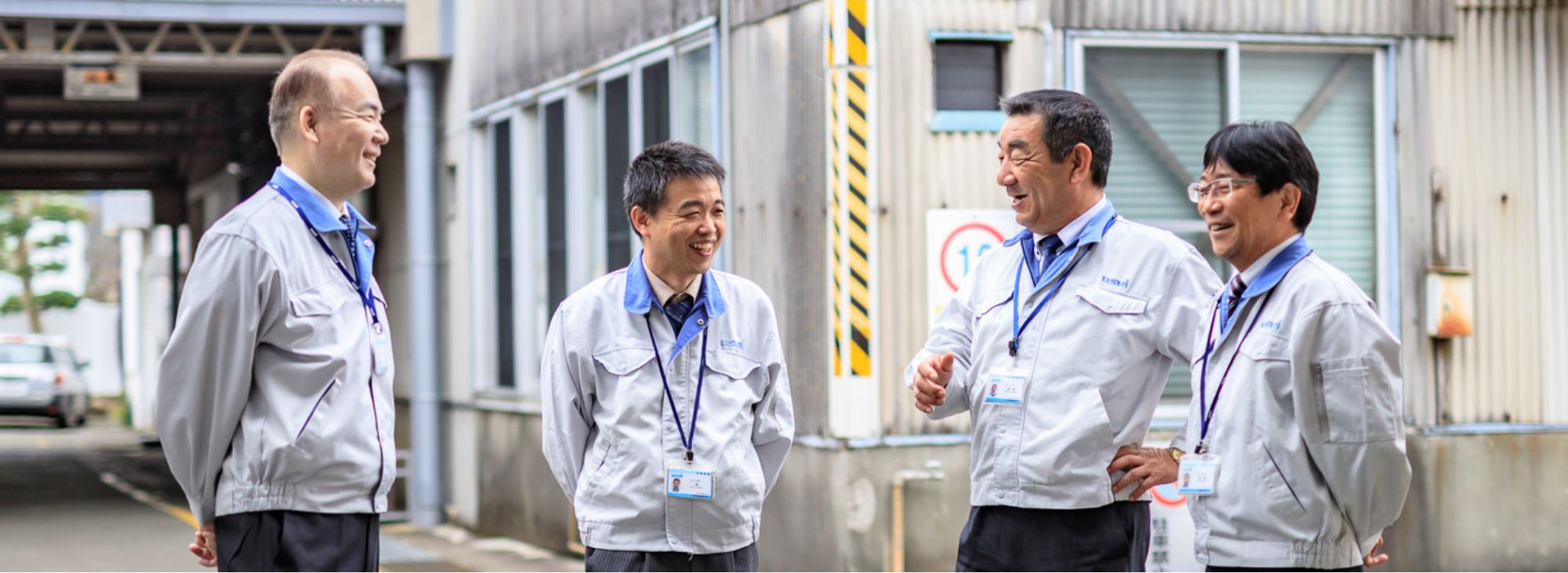
水素自動車の市販化がスタートしても、なお続く改善の日々
- 深澤
- FCV用高圧水素配管の話が、最初にお客様から来たのは2009年のことで、水素自動車の発表まで約5年間は週に1~2回は必ずお客様通いでしたから、量産化にこぎつけた時には営業としては「やっと肩の荷が降りた」とホッとしましたね。
- 林
- 実際に量産化に向けた細かな折衝は最後まで繰り返されましたね。私が「ようやく決着がついたかな」と実感できたのは、2014年の水素自動車発売の直前のことでした。
- 堤
- スタートから約5年、真っ只中にいる時はあまり感じませんでしたが、こうして振り返ると本当に長い期間携わっていたんですね。
- 渡邊
- でも漏れの情報は製造部門に来ますので、私としては市販がスタートしても、肩の荷が降りたとは感じられなかったですよ(笑)。
- 林
- 漏れに関して当社に起因するケースは少ないけど、なぜか話が一番持ち込まれやすいからね。
- 渡邊
- ただそれらはいわゆるクレームではなくて、品質をより向上させるための貴重な情報でしたから、こうした経験の蓄積はその後にしっかり生かされていると思います。
- 深澤
- 世の中の誰もが手掛けたことのない製品でしたから「販売にこぎつけたからこれで安心」とはならず、今後も継続して高い品質を維持しなければならないというプレッシャーも、一方ではありましたよね。
「正しい答え」を誰も知らない、未知への挑戦を経て
- 林
- そもそも水素自動車というものが世の中になかったので、一つ一つの解決方法が果たして正しいのかどうかが誰にもジャッジできなかった。そこが他の製品との最大の違いでした。ですからある意味で「量産化しても終わらない製品」であり、実際にいまだに改善が繰り返されていますからね。
- 堤
- 私たちにとっても、本当に「未知の領域へのチャレンジ」でしたね。
- 渡邊
-
水素自動車は、東京オリンピックで運行された水素自動車のバスが普及の一つの契機になったんじゃないでしょうか。
あのバスが話題になったことで世間での認知度も上がりましたよね。
- 林
-
バスについてはまた大変なことも多かったんですが(笑)。
長短数多いパイプ製品を組み込んだ上で、車両に搭載されている様々な機器に合わせて一切の誤差もなくキッチリと収めるのには本当に苦労しました。
- 渡邊
- 発表当時の自家用車に使用された高圧水素配管は6本でしたが、バスではそれが1台あたり50本以上ですからね。
- 林
-
このFCV用高圧水素配管プロジェクトは、今振り返っても本当に大変なことの連続でした。
ふだんお客様とはいつもスムーズにやり取りしていますが、この時ばかりは本当に喧々諤々でしたからね。
でもこのプロジェクトで得た「終わりなき挑戦」の経験は、当社にとってはかけがえのない貴重な財産になったんじゃないかと思います。
- 深澤
- 今後エコカーとして水素自動車がどう成長していくのかはまだわかりませんが、2035年以降、水素自動車がメインストリームの一角を占めるようになれば、この苦労も報われるのではないかと期待しています。
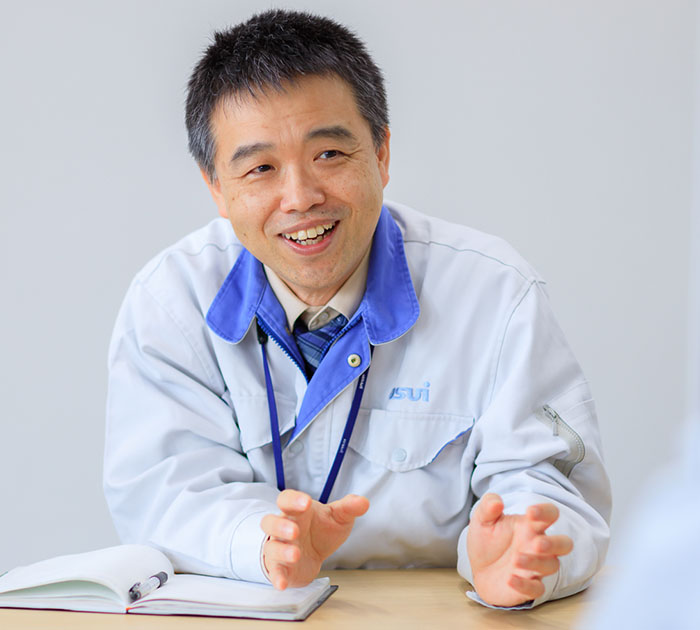
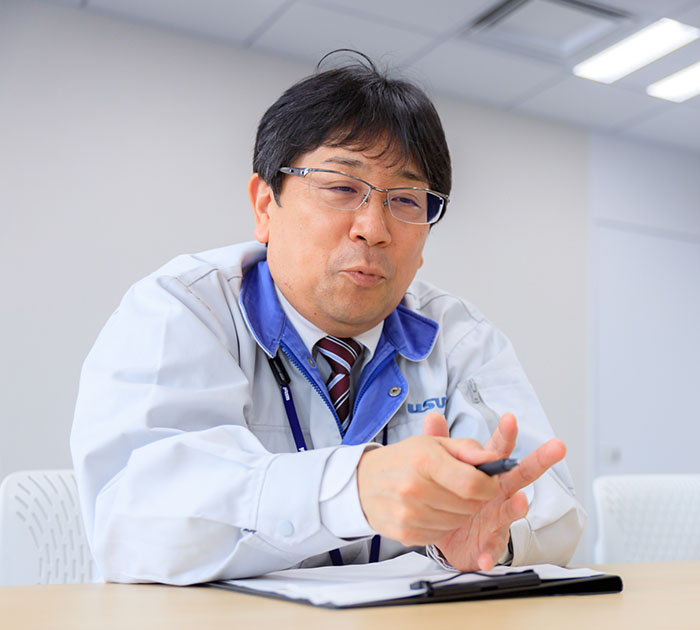
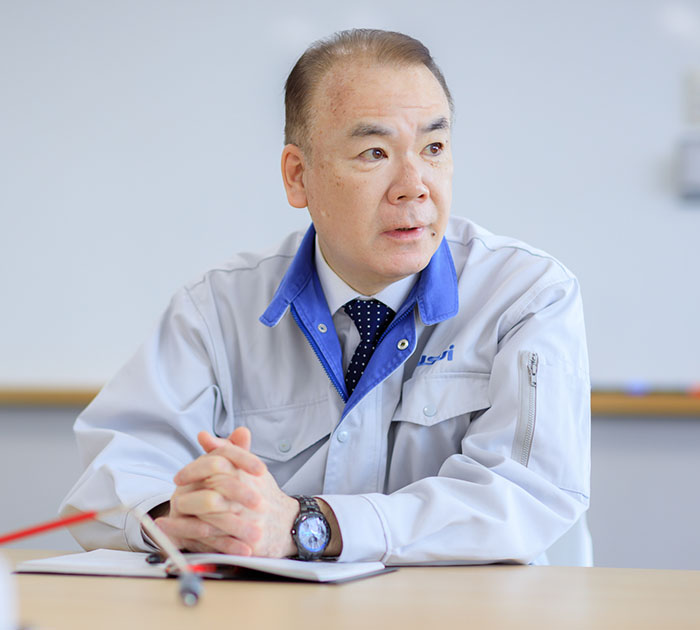
おわりに
水素自動車のタンクに入る水素の量は約4kg。このタンク内の水素は700気圧という高圧で圧縮されており、ひとたび通常の1気圧下におかれるとその容積が800倍へと急膨張するという非常に大きなエネルギーが封じ込められています。
万が一にもこの高圧気体の漏洩による危険を招くことのない、高い安全性を実現したこのプロジェクトは、USUIが手掛ける製品の際立った重要性を雄弁に物語るものだったと言うことができるでしょう。
内燃機関を中心に信頼を勝ち取ってきたUSUIの製品は、どの一つを取ってもみな安全性の高さを求められる重要保安部品です。
お客様も未知数、当社も未知数の中で、プロだからこそできる「より良いモノづくり」を模索したこのプロジェクトで培われた価値ある経験を糧として、USUIではこれからも関連部署の様々な立場の関係者が携わり、「当社にしかできないモノづくりのあり方」をきっと実現させ続けていくことでしょう。